A Guide to Horizontal Flow Wrappers
Helping You Avoid Inconsistently Wrapped Products & Ultimately Save on Production Costs
A horizontal flow wrapper wraps your product with a single roll of film by using a former to guide the film around the product and then trimming or sealing any excess film below the center of the product. Rollers below the table, called fin seal wheels, heat and compress the film ends to create a longitudinal seal. The wrapper then uses sealing jaws to seal the back of one product while also creating the front of another. This continuous cycle will streamline your production while also creating consistently wrapped products.
In this horizontal flow wrapper guide, we will cover,
- How the machine operates
- Different types of infeeds
- Print registration
- Types of formers
- Types of end seals
- Terminology commonly used
- Recommended manufacturers
How a Horizontal Flow Wrapper Operates
The operation of a horizontal flow wrapper first begins with wrapping your product completely with film. Your product will be delivered by an infeed conveyor while the film tube is being formed around it, this is when a fin seal is created. Next, your product will then move to a cutting head, this is where the end seals are created and cut from the adjoining wrapped product. Lastly, your product will move along to the discharge area and then proceed throughout the rest of the packaging process.
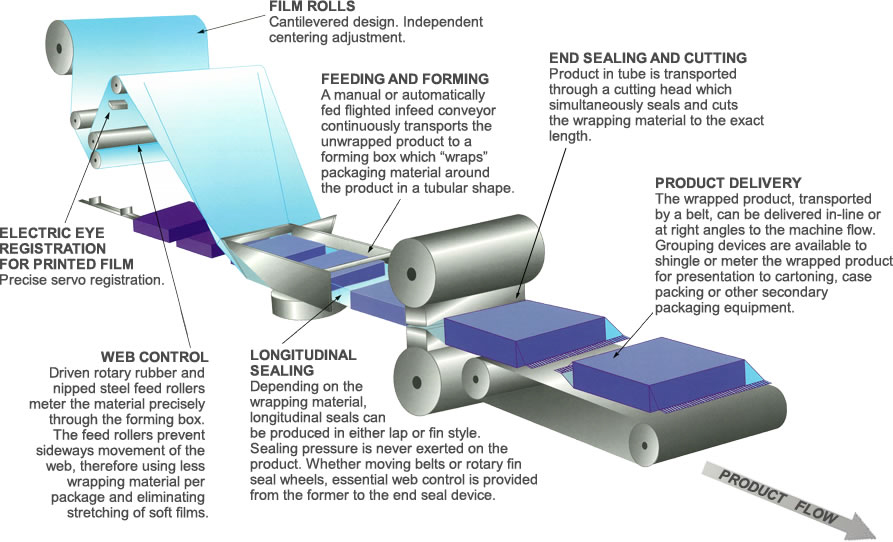
Photo Source: https://drflexpac.com/flow-wrap-film/
Different Types of Infeeds
There are several different types of infeeds to fit whatever kind of product you’re running. If you’re unsure of what kind of infeed would fit best with your product, we recommend sending in samples so our equipment experts can inspect them and provide a recommendation for best practice.
Lugged Infeed
This type of wrapper helps move your product through the conveyor to the former head where it will then be cut. An example of this is shown with our Doboy Mustang IV Print Register Flow Wrapper. As you watch the video, you will see that the product is in between the lugs before it’s pushed through to be wrapped. It will then go through the forming head and then the sealing jaws.
Elevated Lug Infeed
This style of wrapper elevated the product slightly as to reduce friction between the product and the table. Below is a video example of a Bosch 301 Print Registered Wrapper in production.
Belt Infeed
This type of wrapper focuses on sealability, making it ideal for food and medical products. Belt infeeds create high-quality seals and the ease of threading the film through it creates a seamless user experience.
Print Registration
Print registered machines have a photo eye located on the dancer bar and its job is to look for and confirm register marks. Print registration helps with the quality control of your products and ensures that all printed images are in the exact same location on every package every time. This is key for consistency and brand image. If your products are being packaged with a logo or other important information on them, you will want to make sure your wrapper has print registration features.
Types of Formers
Fixed Former
Fixed formers are made specific to a product’s width, so you can adjust depending on what your product weight is, but the width is not adjustable. When purchasing one of these formers, we suggest sending us samples of your products so that we can ensure it will run correctly.
Adjustable Former
The adjustable former is suitable to run different sized products and is great for companies that are changing production from month to month and need more flexibility.
Types of End Seals
So once your product has gone through the former on your flow wrapper, it’s ready for an end seal. Here are the different types of end seals you’ll be working with.
Rotary Motion
This end seal works well with high-speed production, but due to the speed, is compatible with a limited range of product lengths and widths.
Box Motion
Is a different type of cutting motion that operates at a lower speed but offers the flexibility of working with a wide range of product lengths and widths.
Terminology commonly used
Below are some common terms that are used to describe a horizontal flow wrapper and the sealing functions they perform.
Number Up - this refers to the cutting head configuration and will signify the number of seal jaws that are on the shaft
Fin Seal - this is also referred to as the fold-over seam and happens when both interior edges of the film are sealed together and then the fin is folded over
Long Dwell - this extends the time that the heated jaws are in contact with the film. The goal of this is to achieve an airtight seal which is ideal for perishable products or when working with thicker films.
Recommended manufacturers
Manufactures of the horizontal flow wrapper that we recommend are as follows
- Bosch
- PFM
- Formost Fuji
- Hayssen
- Ilapak
- Ulma
Summary
The goal of incorporating a horizontal flow wrapper into your production is to achieve consistent and efficient packaging. Using a flow wrapper helps you avoid inconsistently formed or loosely wrapped products that will result in poor appearance and loss of money.
To view our selection of horizontal flow wrappers, click here. If you still have questions and would like to talk to a member of our sales team, please reach out by clicking the button below.
Contact