A Guide to Depalletizers
Increasing Production Times and Improving Efficiencies
Depalletizers are designed to quickly remove cases, bags, bottles, cans, and other containers from a pallet. This allows manufacturing facilities to automate their processes and quickly remove wholesale materials from their pallets and prevent repetitive workplace injuries.
In general, the act of “depalletizing” is the process of releasing stacked layers of product from a pallet and placing them directly on the production line. Some depalletizers have the ability to unload multiple pallets at once, or can simultaneously load and unload pallets at the same time.
Topics:
- Industries
- Manufacturers
- Where a Depalletizer Fits Into a Production Line
- High vs Low-Level Depalletizer
- Transfer Methods
- Downstream Equipment
- Dunnage
- Questions to Consider Before Purchasing or Selling
- Configuring a Depalletizer for Your Facility
Industries:
Common industries that utilize a depalletizer are:
- Chemical
- Beverage.
- Household goods,
- Fulfillment centers.
Food
Depalletizers, by definition, are designed to remove pallets quickly. They're designed to remove cases, bags, and bottles in cases quickly from a pallet by releasing the product stack and placing it onto the product line.
Manufacturers:
Featured manufacturers that we see are
- BW Integrated/Fleetwood
- KHS
- Sentry
- Whallon
- ABC
- Arrowhead
- Honeywell/Alvey
- Premier Tech
High Level vs Low-Level Depalletizer:
Now that we've seen manufacturers, let's talk about low and high-level depalletizers. The best way to differentiate between the two categories is by the container discharge. This simply means that some equipment will discharge the materials at a specific height based on your facility's needs. Some facilities need the materials to be removed at floor level, and a low-level or floor level depalletizer is needed. For those who need material to go into a hopper or a part of the production line that is off of the ground, they will need a high-level depalletizer.
Where Depalletizers Fit in a Production Line:
When deciding if you need a depalletizer, you will need to consider where the equipment will live in your facility. This means knowing where to place the equipment in your production line. Typically these machines are at the beginning of a filling process as they take the materials from other vendors and add them to the production line.
The diagram below shows how a depalletizer removes materials and then places them on a conveyor or accumulation table to move down the production line.
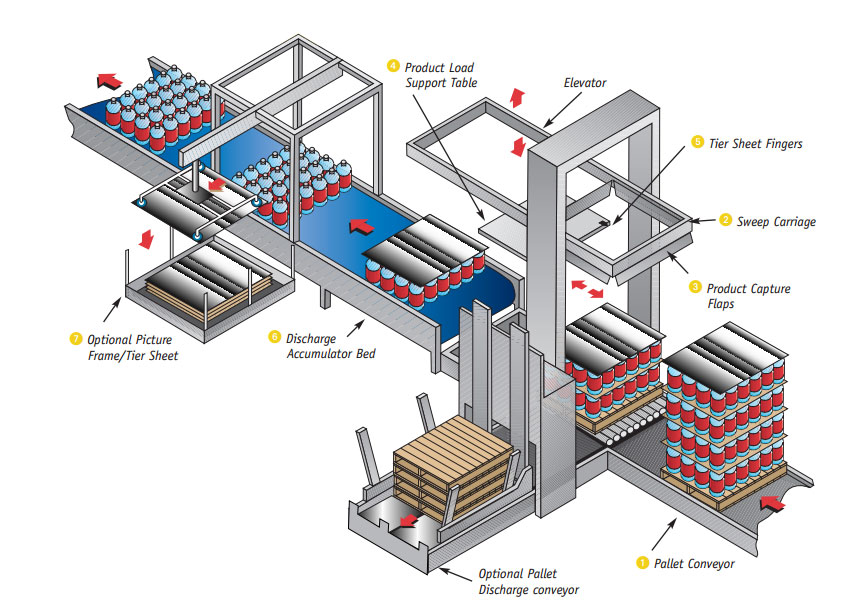
Transfer Methods
The reason for the different styles of removing heads is the different types of products that are being added to the production line. There are three main ways that depalletizers transfer products from their shipped pallet to the production line. Those are:
- Magnetic
- Robotic
- Sweep
Magnetic:
The magnetic depalletizer uses a magnetic plate to grab the tops of magnetic material, similar to metal lids to glass bottles, and picks up the tops of the equipment and places them safely into the next phase of production. These machines can also have the optional feature to remove tier sheets.
A tier sheet is a plastic sheet added between layers of palletized materials to keep them in place. They are primarily used in the beverage industry and are reusable.
Robotic
Next is the robotic method that uses the robotic arm to depalletize supplies. This process uses a robotic arm to grip the pallet and remove the tier sheet first. It then places the materials in the designated area. This is so the materials are not damaged during this stage.
Sweep
The most common method is the sweep method. This machine pulls the pallet onto the conveyor and removes the tier sheet. It then uses a sweeping arm to “sweep” the materials off of the pallet and into the production line.
Downstream Equipment
Downstream equipment includes:
- Decasing equipment if necessary
- Rinsing and cleaning equipment
- Unscrambling
- Accumulation tables
- Filling
- Capping
- Labelers
- Case erecting, packing and sealing equipment
- Palletizers
- Stretch wrappers
Dunnage
Something to consider is the dunnage or the straps, plastic, tier sheets that go between the layers, and even the wooden layers that have to be strapped to something stronger than plastic to keep the load stable.
If your facility needs these materials as a part of receiving the materials you will need to confirm that your depalletizer will be able to handle that. Typically, facilities have at least one operator managing and removing those things, but if you need to automate it, you will need to note that when looking for the right machine.
Questions to Consider
Whether you are buying or selling your machine, consider the questions below. If you are selling equipment, these are the answers we need before scheduling a visit. If you are buying, these questions will help you find the right machine for your needs.
What type is it?
- Is it a high or low-level depalletizer?
- What type of containers?
- Glass, metal, plastic, or other applications?
- The products last ran
- The Maximum load, height and weight and speed, and sweeps per minute.
- What type of transfer method does it have?
- Is it a robot, robotic, magnetic, or sweep?
- Available floor space?
Additional questions include
- Electrical requirements
- Your electrical requirements
- What optional features do you need?
- Is there an operation or mezzanine?
- Is it servo-driven?
- Empty pallet conveyor or tier sheet remover
Configuring a Depalletizer for Your Facility:
Most depalletizers are used in high-production facilities most depalletizers are used in high-production facilities so you will need to make sure that the equipment will fit with your operations. Not only is this a machine that has a large footprint for your facility, but it also has to be configured and assembled to your specifications. That’s why when buying used, you will want to make sure that your rigging and removal team can set it up exactly how they removed the equipment.
You will also want to coordinate with your logistics team to ensure that the pieces are being stored and skidded and shipped properly as these machines can be susceptible to damage.
Conclusion:
A depalletizer is a great way for you to automate your production process and help keep workplace injuries low. If you are looking to purchase your next depalletizer from SIGMA Equipment, or want to discuss your next project contact us at the button below.
Contact